Plastic extrusion used in building, transport, and more
Understanding the Fundamentals and Applications of Plastic Extrusion in Modern Manufacturing
In the world of modern production, the method of plastic extrusion plays a critical role - plastic extrusion. This complex process, entailing the melting and shaping of plastic with specialized dies, is leveraged throughout numerous markets for the production of diverse products. From vehicle components to consumer goods packaging, the applications are huge, and the potential for sustainability is equally outstanding. Untangling the principles of this procedure exposes real versatility and possibility of plastic extrusion.
The Basics of Plastic Extrusion Process
While it may show up complicated, the basics of the plastic extrusion process are based on relatively uncomplicated principles. It is a production process in which plastic is melted and then formed into a continual profile through a die. The plastic extrusion procedure is extensively made use of in various industries due to its cost-effectiveness, adaptability, and effectiveness.
Different Types of Plastic Extrusion Methods
Structure upon the basic understanding of the plastic extrusion procedure, it is essential to check out the different methods associated with this production technique. The two key techniques are profile extrusion and sheet extrusion. In account extrusion, plastic is melted and developed into a constant account, usually used to create pipelines, rods, rails, and window frames. In comparison, sheet extrusion produces big, level sheets of plastic, which are generally further refined into products such as food product packaging, shower drapes, and car components. Each method calls for specialized machinery and precise control over temperature and pressure to make certain the plastic maintains its form throughout cooling. Recognizing these strategies is essential to using plastic extrusion successfully in modern manufacturing.
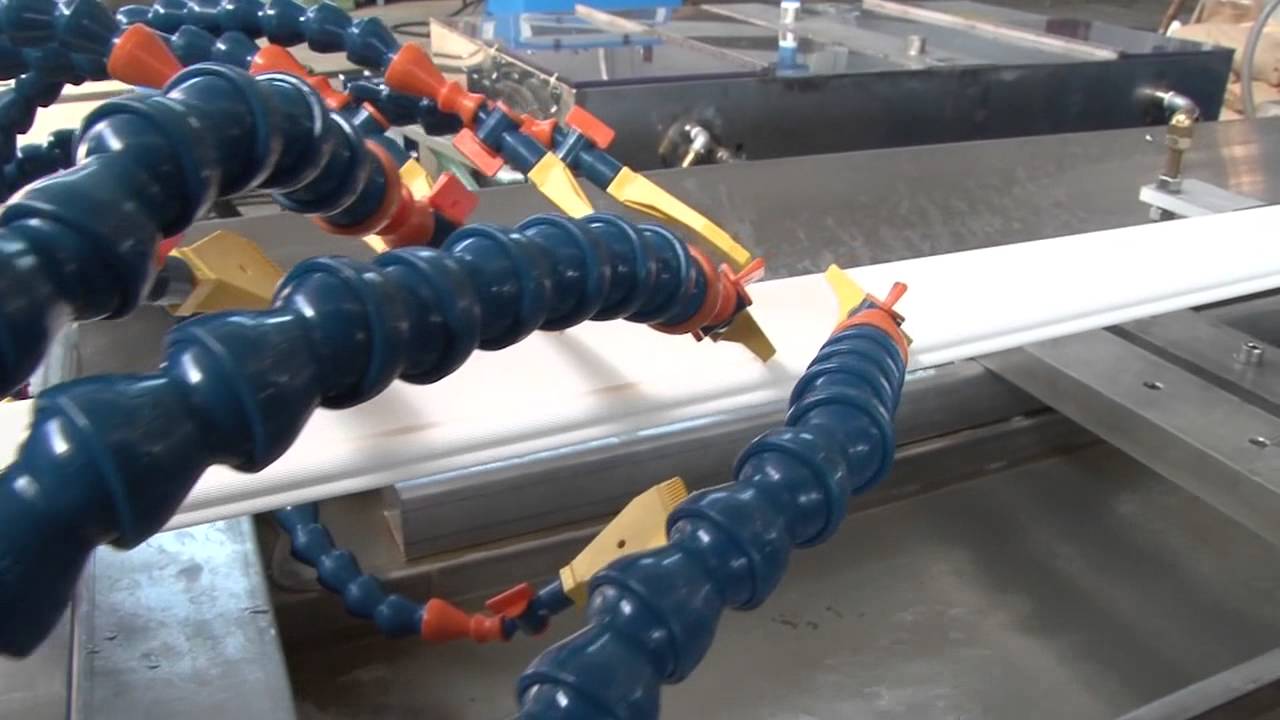
The Role of Plastic Extrusion in the Automotive Industry
A frustrating majority of parts moved here in contemporary automobiles are items of the plastic extrusion procedure. Plastic extrusion is primarily utilized in the production of different car parts such as bumpers, grills, door panels, and control panel trim. Thus, plastic extrusion plays a pivotal role in vehicle production.
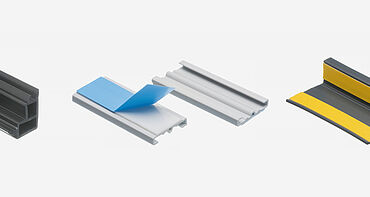
Applications of Plastic Extrusion in Durable Goods Manufacturing
Beyond its substantial influence on the vehicle industry, plastic extrusion proves similarly reliable in the world of customer items producing. The adaptability of plastic extrusion allows makers to make and generate complex forms and sizes with high accuracy and performance. The versatility, flexibility, and cost-effectiveness of plastic extrusion make it a recommended option for lots of consumer goods makers, contributing considerably to the market's development and advancement.
Environmental Effect and Sustainability in Plastic Extrusion
The prevalent use plastic extrusion in making welcomes analysis of its environmental effects. As a process that frequently makes use of non-biodegradable materials, the environmental influence can be significant. Energy usage, waste production, and carbon exhausts are all concerns. Sector innovations are increasing sustainability. Efficient machinery minimizes power use, while waste management systems recycle scrap plastic, lowering basic material needs. In addition, the advancement of naturally degradable plastics supplies a more environmentally pleasant choice. Despite these renovations, even more advancement is needed to check my source reduce the environmental footprint of plastic extrusion. As culture leans in the direction of sustainability, makers read the article need to adapt to continue to be sensible, stressing the value of constant research and innovation in this area.
Verdict
In final thought, plastic extrusion plays a crucial function in modern-day manufacturing, especially in the automobile and consumer products markets. Recognizing the essentials of this procedure is vital to optimizing its advantages and applications.
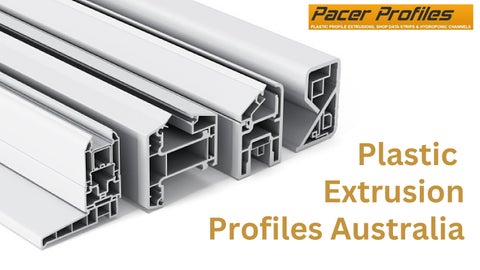
The plastic extrusion process is extensively made use of in different markets due to its cost-effectiveness, convenience, and efficiency.
Building upon the standard understanding of the plastic extrusion process, it is needed to check out the various strategies included in this production method. plastic extrusion. In comparison, sheet extrusion produces big, level sheets of plastic, which are commonly further refined right into products such as food product packaging, shower drapes, and vehicle components.An overwhelming majority of components in modern lorries are products of the plastic extrusion process